Closing the loop
Making material reuse automatic in commercial construction
In commercial projects using Cradle to Cradle (C2C) certified products, there's no reliable system to track where materials go or to bring them back. I designed C2C Manager to make circularity not just possible, but practical.
Timeline
March-April 2025
Status
Concept prototype
My role
UX & Product Designer
(concept, research, UX flows, UI, prototyping)
Team
Solo project.
Informed by past experience + industry discussions
Impact
If implemented, C2C Manager could:
- Cut waste by increasing material reuse
- Save time through automated logistics
- Support reporting needs for sustainable certification

Making circular construction the easiest choice means starting with better systems
Certified building materials are designed to be reused, but most end up in landfills. Why? Because no one owns the tracking process. Once materials are installed, they're forgotten.
Architects move on. Contractors wrap up. Building managers inherit assets with no context. Suppliers rarely get called to reclaim anything.
Circularity isn't broken because of bad intentions, it's broken because there's no system to make reuse simple.
Where reuse breaks down:

How might we make reuse easy from day one, not just at handover?
Most circularity efforts start too late — during demolition or post-construction audits. With Loopa, I designed a system that begins at the point of material specification. The goal was to make reuse planning automatic, not additional.
To figure out how and when reuse should be tracked, I mapped out three possible flows.
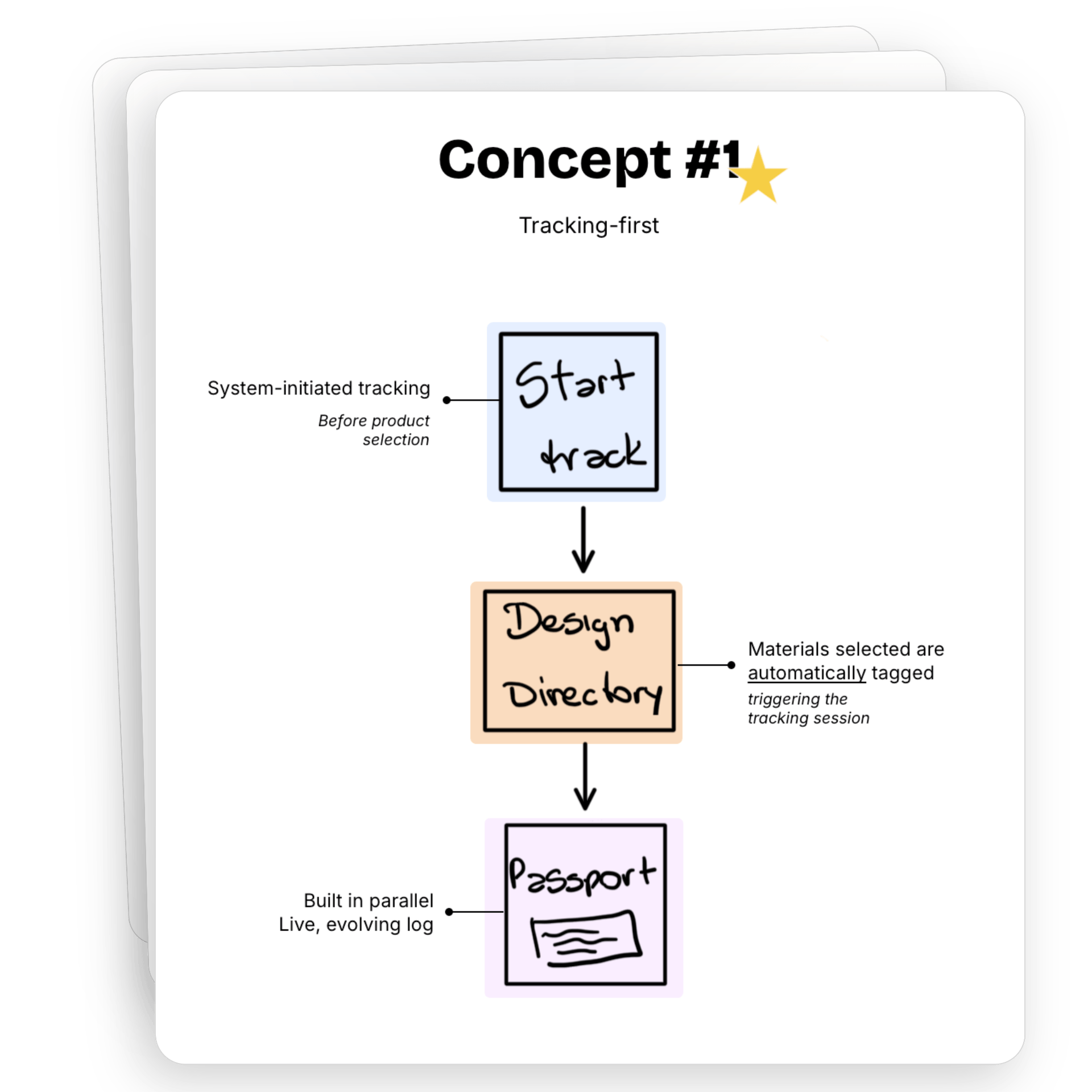
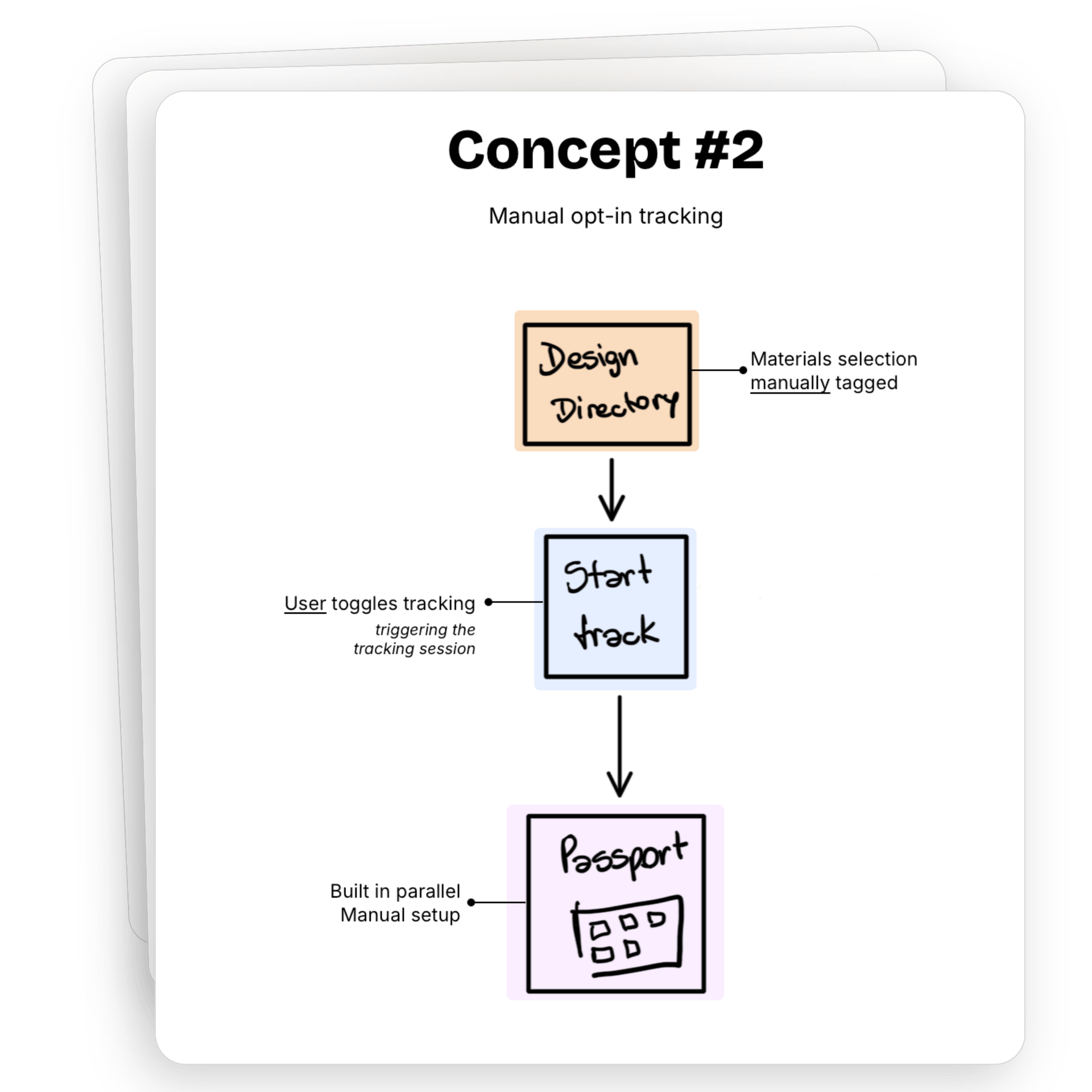
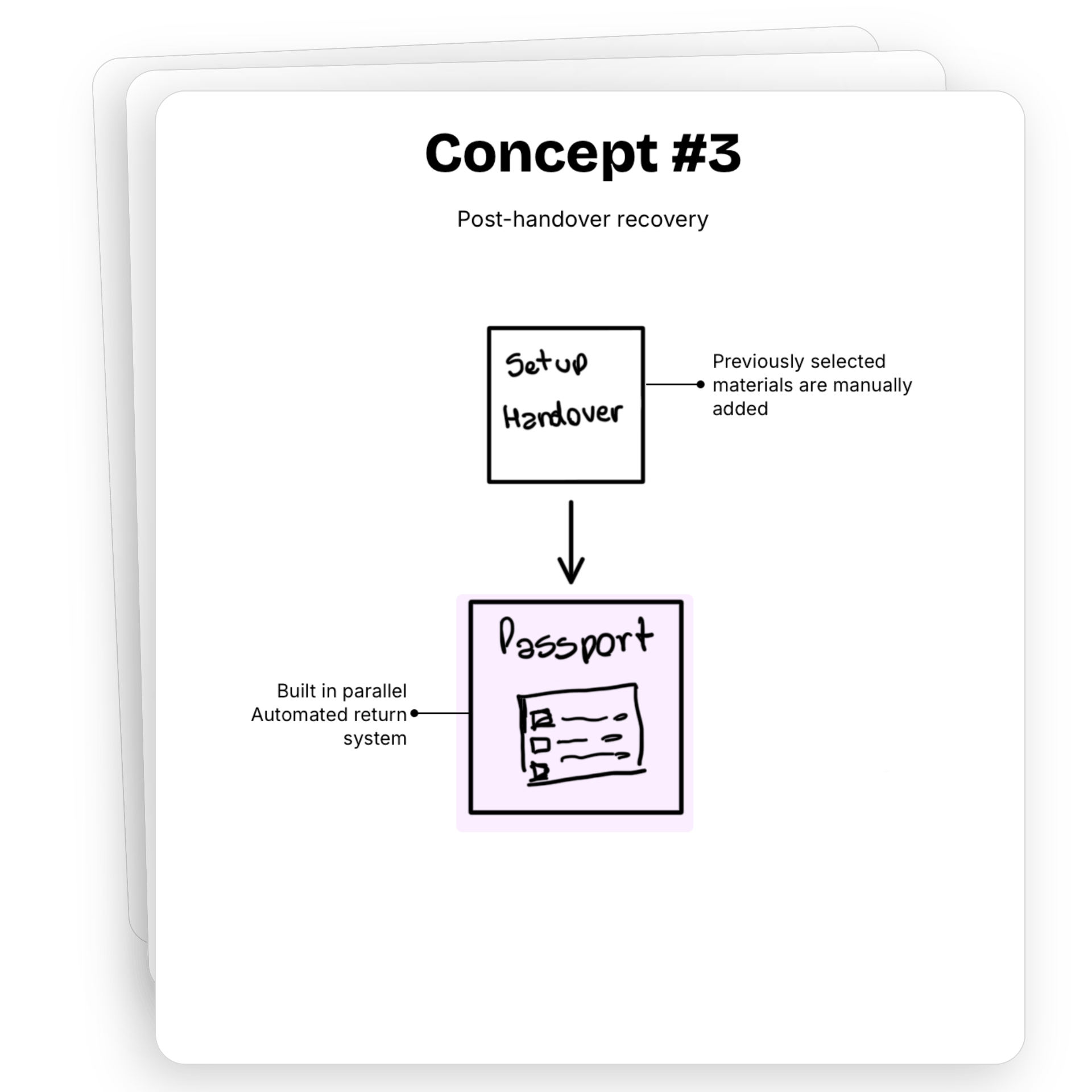
Concept #1 became the foundation for Loopa's final design, a system where reuse starts early and builds value silently in the background.
I translated this logic into two core user flows:
- Selecting certified materials via the Loopa Directory
- Managing and returning them through a live project log — the Loopa Passport
These tools were designed to feel light and familiar, while carrying critical data through every phase of a project.
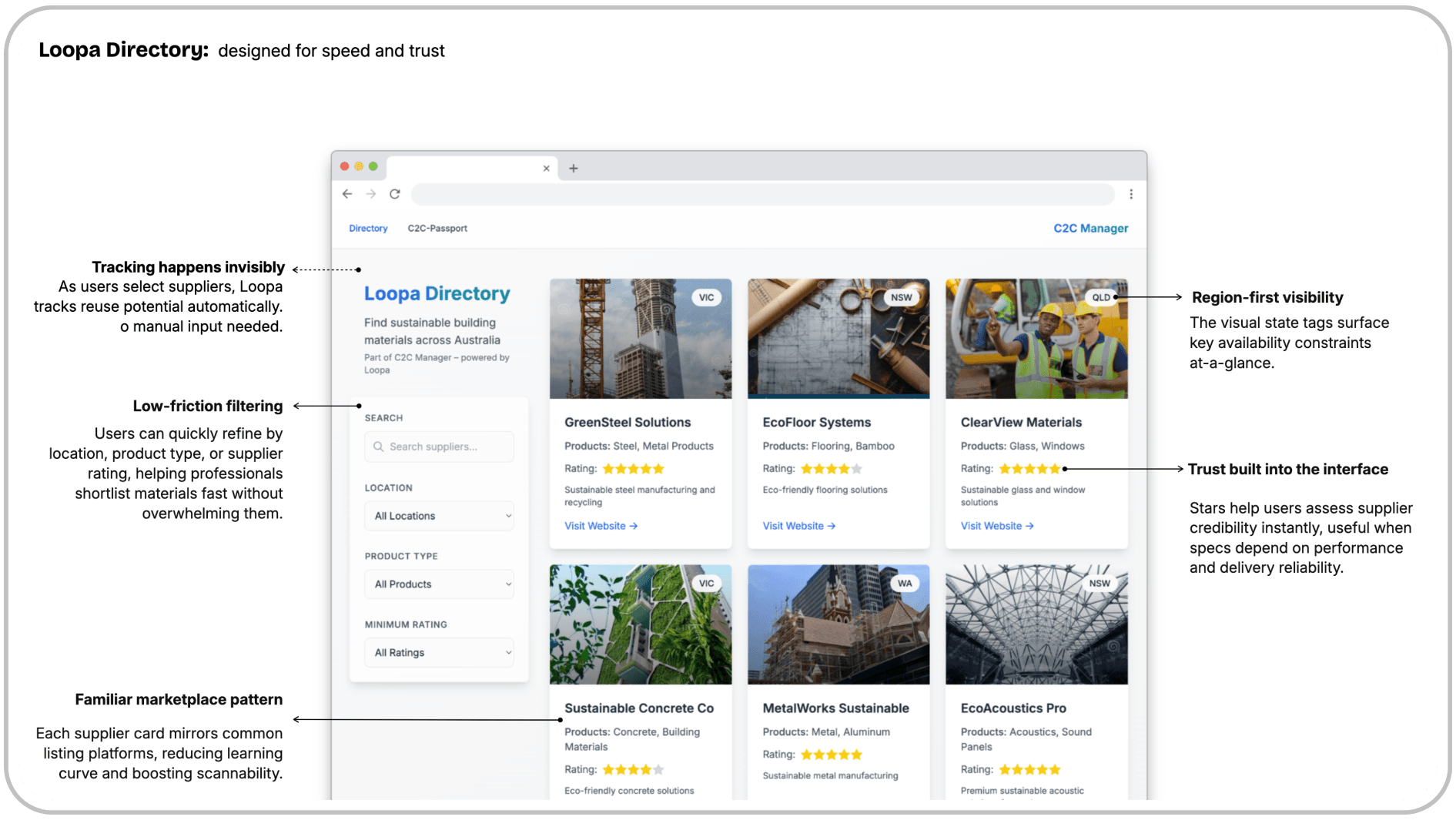
A familiar marketplace layout lets architects quickly find certified materials. Filters reduce friction, regional tags aid sourcing, and star ratings build supplier credibility, all while tracking happens invisibly in the background.
How the tools come together to deliver real impact
Together, the Directory and Passport make reuse easy to follow through. Architects can track without extra steps. Managers can hand off with confidence. And suppliers finally get notified, not forgotten.
This isn't just about managing data. It's about enabling action across roles, at the right time — without anyone needing to think about tracking.
Loopa is still a concept, but the problem is real.
I'm actively exploring how this idea could evolve, and open to collaboration with material suppliers, sustainability teams or construction tech platforms.
What I learned, and what I'd explore next
This project sharpened my skills in systems thinking, complex workflow design, and designing for sustainability at scale, translating industry pain points into actionable digital solutions.
The idea for Loopa emerged from repeated conversations with fellow architects and suppliers. I noticed a common frustration: sustainable materials were often specified, but rarely reclaimed. The beginning and end of the process felt disconnected, and no one truly owned the handover.
Designing Loopa gave me a way to turn insight into action. If I were to continue, I'd test how the product performs in retrofit and shared asset environments and actively seek partnerships with material suppliers, sustainability teams, and construction tech platforms to bring it into the real world.